Section 00-04: Noise, Vibration and Harshness | 1993 Mustang Workshop Manual |
DIAGNOSIS AND TESTING
Noise, Vibration and Harshness
Tools Required:
- Rotunda Radial Run-Out Gauge 007-00014
- Belt Tension Gauge T63L-8620-A
- Dial Indicator with Bracketry TOOL-4201-C
These diagnosis charts are designed to take the technician through a
step-by-step diagnosis procedure to determine the cause of a condition. It may
not always be necessary to follow chart to its conclusion. Perform only the
Steps necessary to correct the condition. Then check operation of the system to
ensure the cause has been found.
It is sometimes necessary to remove various components of vehicle to gain
access to component to be tested. Refer to applicable Section for removal and
installation of components. After verifying the condition has been corrected,
ensure all components removed have been installed.
PINPOINT TEST A: HIGH SPEED SHAKE DIAGNOSIS
A1 ROAD TEST
- Accelerate vehicle to the speed which the customer indicated the shake occurred.
No
Vehicle OK.
Yes
GO to A2.
A2 INSPECT TIRES
- Raise vehicle on hoist. Inspect tires for extreme wear or damage, cupping or flat spots.
Are tires OK?
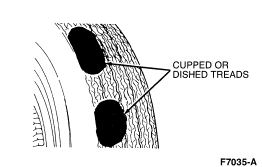
Yes
GO to A3.
No
CHECK suspension components for misalignment, abnormal wear, or damage that may have contributed to the tire wear. CORRECT suspension concerns, and REPLACE damaged tires. PERFORM Road Test.
A3 INSPECT WHEEL BEARINGS
- Spin front tires by hand to check for wheel bearing roughness. Check bearing end play.
Is end play OK?
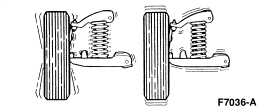
Yes
GO to A4.
No
ADJUST or REPLACE and lubricate bearings as necessary. PERFORM Road Test.
A4 WHEEL/TIRE RUNOUT ON VEHICLE
- Measure wheel/tire assembly runouts on vehicle using Rotunda Radial Run-Out Gauge 007-00014 or equivalent. Assembly runout should be less than 1.14 mm (0.045 inch) radial and lateral. Warm up tires prior to taking measurement to eliminate slight fla
Is measurement in specification?
Yes
GO to A9.
No
GO to A5.
A5 WHEEL/TIRE RUNOUT OFF VEHICLE
- Measure wheel/tire assembly from any position that exceeds 1.14 mm (0.045 inch) radial or lateral. Before removing wheel/tire assembly, mark wheel stud and corresponding bolt hole so assembly can be installed in same position. Remove assembly and mo
Is measurement in specification?
Yes
CHECK rotor drum and bolt circle runout. GO to A8.
No
GO to A6.
A6 MATCH MOUNTNG
- Mark the high runout location on the tire and also on the wheel. Break the assembly down and rotate the tire 180 degrees (half-way around) on the wheel. Inflate the tire and measure the runouts.
Proper balance achieved
BALANCE assembly and INSTALL on vehicle. PERFORM Road Test.
Improper balance
If high spot is within 101.6mm (4 inch) of first high spot on the tire, REPLACE tire. BALANCE assembly and INSTALL on vehicle. PERFORM Road Test.
Improper balance
If high spot is not within 101.6mm (4 inches) of first high spot on the tire, GO to A7.
A7 WHEEL RUNOUT
- Dismount tire and mount wheel on wheel balancer. Measure runouts on both flanges. Runout should be less than 1.14 mm (0.045 inch) radial and lateral.
Is there proper runout?
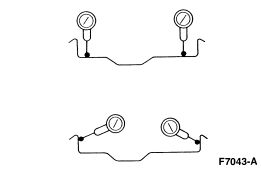
Yes
LOCATE and MARK low spot on wheel and INSTALL tire matching high spot on wheel. BALANCE assembly and PERFORM Road Test.
No
REPLACE wheel. CHECK runouts on new wheel. If new wheel is within limits, LOCATE and MARK the low spot. INSTALL tire, matching high spot of tire with low spot of wheel. BALANCE assembly and INSTALL on vehicle. PERFORM Road Test.
A8 AXLE, ROTOR OR DRUM AND BOLT CIRCLE RUNOUTS
- For rear wheel positions, remove rotor or drum and measure axle flange face runout (greater than 0.254mm (0.010 inch)). Bolt circuit runout (greater than 0.397mm (0.015 inch)) and drum/rotor pilot radial runout (greater than 0.152mm (0.006 inch)).
- For front wheel positions, measure rotor lateral runout (greater than 0.127mm (0.005 inch)) bolt circle runout (greater than 0.381mm (0.015 inch)) and rotor pilot radial runout (greater than 0.152mm (0.006 inch)).
Are measurements correct?
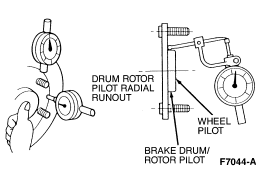
Yes
REPLACE rotor/wheel and PERFORM Road Test.
No
REPLACE rotor (front wheel positions) or axle shaft (rear wheel positions) and PERFORM Road Test.
A9 INSPECT WHEELS
- If wheels are equipped with locking wheel lug nuts, check that proper counter balance wheel weight is installed opposite locking lug nut.
Yes
GO to A10.
No
INSTALL counter. BALANCE wheel weight opposite locking lug nut. PERFORM Road Test.
A10 FRONT TIRES
- Spin front tires with a wheel balance spinner while vehicle is raised on hoist. Feel for vibration in fender or while seated in vehicle.
No
GO to A11.
Yes
BALANCE front wheel(s). PERFORM Road Test.
A11 REAR TIRES
- Engage drivetrain while vehicle is raised on hoist. Carefully accelerate the drive wheels while feeling for vibration.
No
GO to A14.
Yes
GO to A12.
A12 DRIVETRAIN
- Remove rear wheels, secure brake drums, if so equipped by installing wheel lug nuts, reversed. Carefully accelerate the drivetrain while feeling for vibration.
No
BALANCE rear wheels. PERFORM Road Test.
Yes
GO to A13.
A13 REAR DRUMS OR ROTORS
- Remove the brake drums or rotors. Carefully accelerate the drivetrain while feeling for vibration.
No
REPLACE drums or rotors. PERFORM Road Test.
Yes
GO to Driveline Vibration Diagnosis.
A14 WHEEL BALANCE
- Balance all wheels not previously balanced. Road test vehicle.
Yes
Vehicle OK.
No
GO to A15.
A15 SUBSTITUTE WHEELS AND TIRES
- Substitute a known good set of wheels and tires. Road test vehicle.
No
INSTALL the original tire/wheel assemblies, one by one, road testing at each step, until the defective tire(s) is identified. REPLACE tire(s) as necessary and RETEST.
Yes
REFER to Driveline Vibration Diagnosis.
PINPOINT TEST B: TIP-IN MOAN DIAGNOSIS
B1 AIR CLEANER
- Check air cleaner for proper installation of base gasket, lid element and air inlet duct assembly.
Are components properly installed?
Yes
GO to B2.
No
CORRECT condition and PERFORM Road Test. If moan persists, GO to B2.
B2 POWERTRAIN RESONANCE
- Loosen all converter housing-to-engine retaining bolts three-quarter turn and road test. Tighten bolts after test.
Is moan reduced or eliminated?
Yes
CHANGE or INSTALL damper as indicated and RETEST. If moan still persists,
GO to B3.
No
GO to B3.
B3 ENGINE MOUNTS
- Normalize engine mounts by loosening them and, with engine running, shifting transmission from NEUTRAL to DRIVE and back to NEUTRAL. With manual transmission, load engine by slipping clutch in gear. Tighten mounting bolts and road test.
Is moan reduced or eliminated?
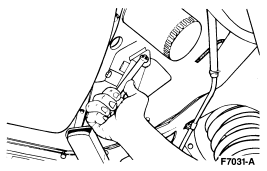
Yes
Vehicle OK.
No
GO to B4.
B4 EXHAUST SYSTEM
- Warm up system to normal operating temperature. Loosen all hanger attachments and reposition hangers until they hang free and straight. Then loosen all flange joints and, with engine running, shift transmission from NEUTRAL to DRIVE and back to NEUTRAL (or load engine with clutch). Tighten all hanger clamps and flanges. Road test vehicle.
Is moan reduced or eliminated?

Yes
Vehicle OK.
No
REFER to Engine Accessory Vibration Diagnosis.
PINPOINT TEST C: DRIVELINE VIBRATION DIAGNOSIS
C1 WHEELS AND TIRES
- Verify that the observed condition is not a high speed shake caused by wheels/tires.
Is observed condition a high speed shake caused by wheels or tires?
Yes
REFER to High Speed Shake Diagnosis for drive-wheel runout and balance procedures.
No
GO to C2.
C2 DRIVESHAFT
- Inspect driveshaft for undercoating or physical damage. Check index marks (yellow paint daubs) on rear of driveshaft and axle companion flange. These marks should be no more than 90 degrees apart.
Are marks more than 90 degrees apart?
No
GO to C3.
Yes
CLEAN off undercoating or REPLACE damaged driveshaft. If index marks are misaligned, GO to C6.
|
|
CHECK for vibration at road test speed. If still present, GO to C3.
|
C3 DRIVESHAFT RUNOUT
- With vehicle on hoist, measure runout at front, center and rear of driveshaft. Maximum runout is 0.89 mm (0.035 inch).
Is maximum runout 0.89mm (0.035 inch)?
Within specification
GO to C7.
At front or center out of specification
GO to C4.
At rear out of specification
MARK the rear runout high point. GO to C5.
C4 DRIVESHAFT RE-INDEXING AT TRANSMISSION
- Note or mark indexing of driveshaft to transmission and axle companion flange. Disconnect the driveshaft, re-index 180 degrees at transmission only and reconnect. Check runout at front and center of driveshaft, maximum runout is 0.89 mm (0.035 inch).
NOTE: While driveshaft is removed from vehicle and manipulate U-joints in each direction of rotation. If a U-joint feels stiff or has a "lumpy", "gritty" feel in any direction, replace U-joints or driveshaft.
Is it within specification?
Yes
CHECK for vibration at road test speed. If still present, mark rear runout high point. GO to C5.
No
GO to C6.
C5 DRIVESHAFT RE-INDEXING AT AXLE
- Note or mark indexing of driveshaft to axle companion flange. Disconnect the driveshaft. Re-index 180 degrees at axle and connect. Check runout at rear of driveshaft. Maximum runout is 0.89 mm (0.035 inch).
Is it within specification?
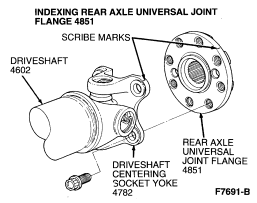
Yes
CHECK for vibration at road-test speed. If still present, GO to C7.
No
GO to C6.
C6 AXLE COMPANION FLANGE
- Compare the two high points of runout marked in Test Steps C3 and C4.
Marks within 25 mm (1 inch) of each other
REPLACE driveshaft. RECHECK vibration.
Marks 180 degrees apart
REPLACE axle companion flange. CHECK driveshaft runout and road test for vibration. If still present, GO to C7.
C7 DRIVESHAFT VIBRATION
- The driveshaft can be re-indexed at both the rear axle and transmission to minimize system imbalance. Refer to driveshaft indexing procedure.
Yes
Vehicle OK.
No
REFER to driveshaft balancing Test Step F1, if vibration still present.
C8 AXLE PINION NOISE DAMPER
- If vibration still exists after balancing driveshaft, install an axle pinion damper, as outlined.
Is vibration still present?
No
REFER to Group 05.
Yes
Vehicle OK. REPLACE driveshaft if vibration still persists.
PINPOINT TEST D: DRIVELINE ANGLES DIAGNOSIS
D1 RIDE HEIGHT
- Check ride height between the axle and rear bumper bracket on frame rail. Refer to Section 04-02.
Yes
GO to D2.
No
CHECK to make sure vehicle is not abnormally loaded. CORRECT ride height if necessary. REFER to Section 04-02. GO to D2.
D2 DRIVELINE ANGLES
Are driveline angles correct?
Yes
GO to D3.
No
CORRECT driveline angles. REFER to Section 04-02. GO to D3.
D3 AXLE RING AND PINION
- If driveline angle corrections do not eliminate vibration, check ring and pinion backlash, refer to Group 05.
Is ring and pinion backlash within specification?
Yes
GO to Pinpoint Test E.
No
ADJUST or REPLACE ring and pinion gearset. REFER to Group 05.
If vibration still exists, GO to Pinpoint Test E.
PINPOINT TEST E: ENGINE ACCESSORY VIBRATION DIAGNOSIS
E1 ENGINE RUN-UP
- Run-up to problem rpm observed in road test, with vehicle stationary.
Yes
GO to E2.
No
PERFORM stall test in DRIVE with brakes locked (or load engine by slipping clutch in gear with manual transmission).
If vibration occurs, GO to Pinpoint Test B.
E2 DRIVE BELTS AND PULLEYS
- With engine stopped, inspect all engine accessory drive belts and pulleys for wear or damage, and check belt tension, using Belt Tension Gauge T63L-8620-A or equivalent.
- Automatic tensioners have belt wear indicator marks. If the indicator mark is not between the min and max marks, the belt is worn or an incorrect belt is installed.
Are belts or pulleys worn or damaged?
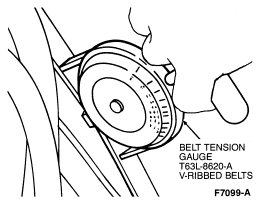
No
GO to E3.
Yes
REPLACE worn or damaged belts or pulleys. CORRECT belt tension. GO to E3.
E3 MOUNTING HARDWARE
- Inspect mounting brackets and adjusting components for proper alignment and tightness.
Are mounting and adjusting components secure?
Yes
GO to E4.
No
ALIGN and TIGHTEN mounting hardware to specifications. CORRECT belt tension. START UP engine and run-up to problem rpm. If vibration still exists, GO to E4.
E4 ENGINE IDLING
- With engine idling, visually check all accessory drive belts and pulleys for misalignment, runout or irregular motion. Maximum runout is 3mm (1/8 inch).
No misalignment visible
GO to E5.
Pulley(s) exceeds maximum runout
REPLACE pulley.
Belt rides up and down on one pulley
REPLACE that pulley.
Belt rides up and down on more than one pulley
REPLACE belt.
E5 ACCESSORY DRIVE BELT NOISE
- Check for "chirps" or squeal in a poly-vee belt by spraying a small amount of water on the grooved side of the belt (use a spray bottle or equivalent).
Yes
CHECK for misalignment. CHECK tensioner position. CHECK for worn belt. SERVICE/REPLACE as required.
No
CHECK accessory bearings. REPLACE as required. GO to E6.
E6 ACCESSORIES
- Run-up engine to problem rpm and, with stethoscope-type device, check each component.
- If the source cannot be detected by probing, remove each belt, one at a time, until vibration goes away.
Is noisy component located?
Yes
REPLACE belt. If vibration still exists, SERVICE or REPLACE component.
No
Possible engine component imbalance. This situation is possible, but unlikely.
PINPOINT TEST F: DRIVESHAFT BALANCE DIAGNOSIS
F1 DRIVESHAFT BALANCING — CLAMP METHOD
- Mark rear of driveshaft in four equal parts and number them 1, 2, 3 and 4.
- Install hose clamp with screw at position No. 1.
- Operate driveline at speed at which customer complained of vibration.
- Rotate clamp to each of the other three positions and check for vibration.
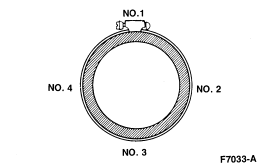
If vibration is worse in all positions
GO to F4.
If vibration is better in any one position
GO to F2.
If vibration is better in any two positions
ROTATE clamp screw to a mid-point between the two positions. GO to F2.
F2 INSTALL SECOND CLAMP
- Install another clamp, with screw in same position as first clamp.
- Operate vehicle at speed at which customer complained of vibration.
Is vibration minimal?
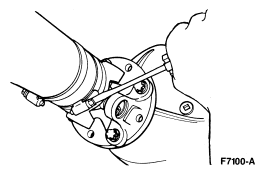
Yes
Condition corrrected.
No
GO to F3.
F3 REPOSITION CLAMP
- Rotate screws of clamps equally away from each other about 12.7mm (1/2 inch).
- Operate vehicle at speed at which customer complained of vibration.
Yes
Condition corrected.
No
GO to F4.
F4 ROAD TEST
- Install wheels and tires.
Yes
Condition corrected.
No
GO to Pinpoint Test A.
PINPOINT TEST G: TIRE/WHEEL RUNOUT
G1 TIRE WHEEL BEARING INSPECTION
- Raise vehicle, inspect tires and check wheel bearings.
Yes
GO to G2.
No
SERVICE bearings. GO to G2.
G2 BALANCE TIRES
- Balance tires and place back on vehicle.
Does vehicle function properly?
Yes
Vehicle OK.
No
GO to G3.
G3 ROTATE TIRES
- Rotate tire and wheel assembly. Front to rear, and rear to front.
Does vehicle function properly?
Yes
Vehicle OK.
No
GO to G4.
G4 CHECK RUNOUT
Radial runout less than 1.01 mm (0.040 inch). Lateral runout less than 1.14 mm (0.045 inch).
In some cases a vibration concern may be caused by tire internal construction inducing force variations which cannot be detected through runout measurement. This condition is diagnosed by installing tire/wheel assemblies (one at a time) from a good vehicle to isolate the offending tire(s). REPLACE tires as necessary. BALANCE tires.
Radial runout more than 1.01mm (0.040 inch)
GO to G5.
Lateral runout more than 1.14mm (0.045 inch)
GO to G6.
G5 INDEX TIRE ON WHEEL
- Index tire on wheel. Align highest runout point to wheel low runout point.
Is total radial runout less than 1.01mm (0.040 inch)?
Yes
GO to G6.
No
GO to G7.
G6 BALANCE TIRES
Yes
Service complete.
No
In some cases a vibration concern may be caused by tire internal construction inducing force variations which cannot be detected through runout measurement. This condition is diagnosed by installing tire/wheel assemblies (one at a time) from a good vehicle to isolate the offending tire(s). REPLACE tires as necessary. BALANCE tires. PERFORM Road Test.
G7 CHECK WHEEL RADIAL RUNOUT
Is wheel runout less than 1.14mm (0.045 inch)?
Yes
REPLACE tire. BALANCE tire. PERFORM Road Test. If still not ok, CHECK radial runout.
No
REPLACE wheel. BALANCE tire. PERFORM Road Test. If still not ok, CHECK radial runout.